Piping System
We provide comprehensive specialized process piping solutions including engineering services such as pre bid engineering, basic engineering, detailed engineering and support engineering which includes engineering of process/ power piping systems for projects, and pre-fabrication services such as cutting and beveling on conventional and CNC machines, welding services on semi-automatic and fully automatic robotic welding machines, conventional and digital radiography, post weld heat treatment using CNG fired fully calibrated furnaces and induction heating process, hydro testing, pickling and passivation, grit blasting (manual and semiautomatic) and painting (manual and semiautomatic). We also specialize in handling complex metals such as varying grades of carbon steel, stainless steel, super duplex stainless steel, alloy steel and other materials including inconel and hastelloy in our manufacturing processes.

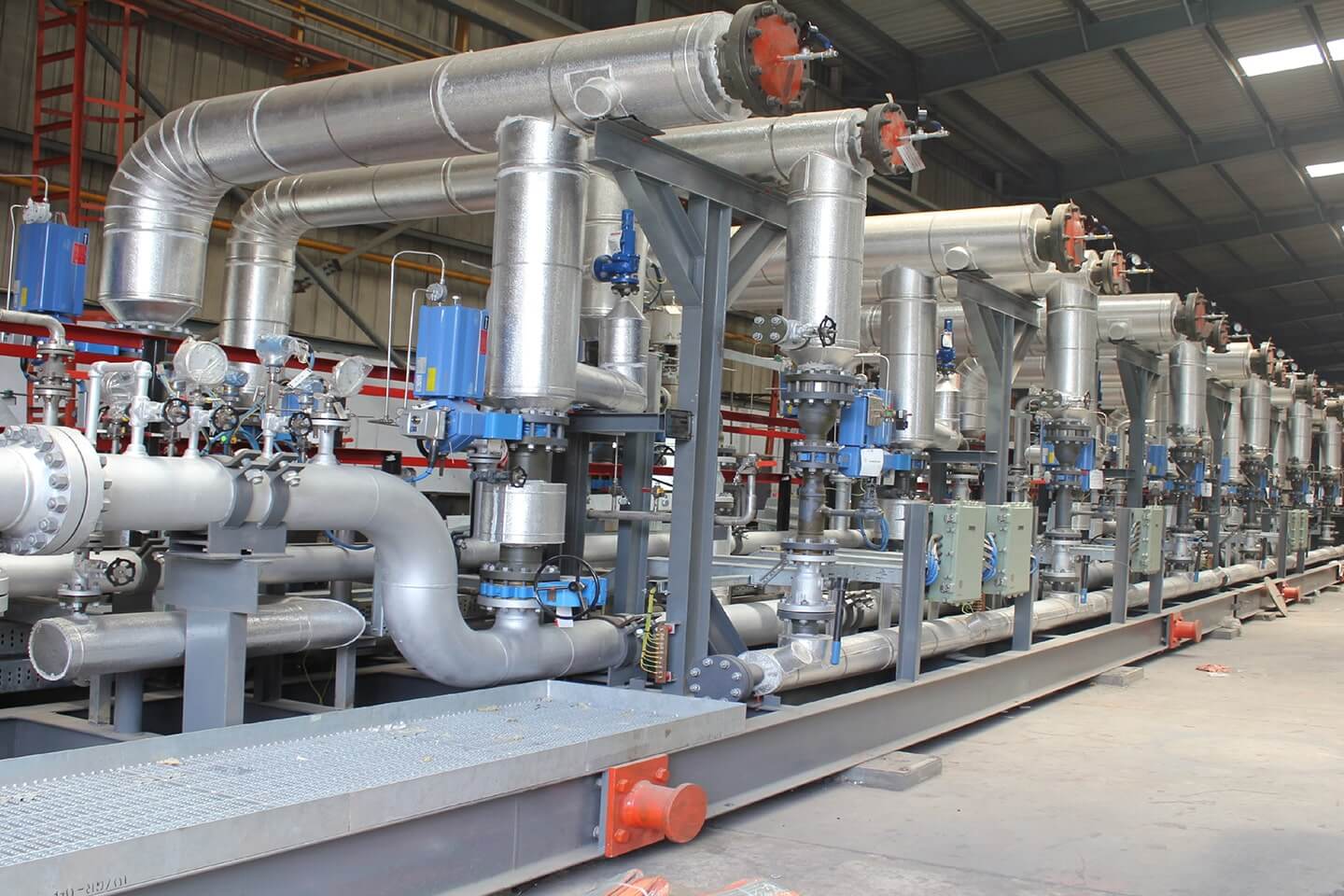
Infrastructure
- We have seven strategically located Manufacturing Facilities at Palwal in Haryana, Anjar in Gujarat, Barmer in Rajasthan, Bangkok in Thailand and Numaligarh in Assam, with three Manufacturing Facilities located at Palwal, Haryana.
- We have a team of 148 quality assurance and quality control engineers and more than 58 employees who are qualified as level II and III NDE personnel from accredited agencies responsible for ensuring quality standards. In executing the projects, we monitor and test all materials for conformity, track non-conformities and make rectifications to ensure customers’ satisfaction. Our quality assurance and quality control team ensure compliance with our quality management systems and statutory and regulatory compliances. This team conducts pre-dispatch inspection of our products.
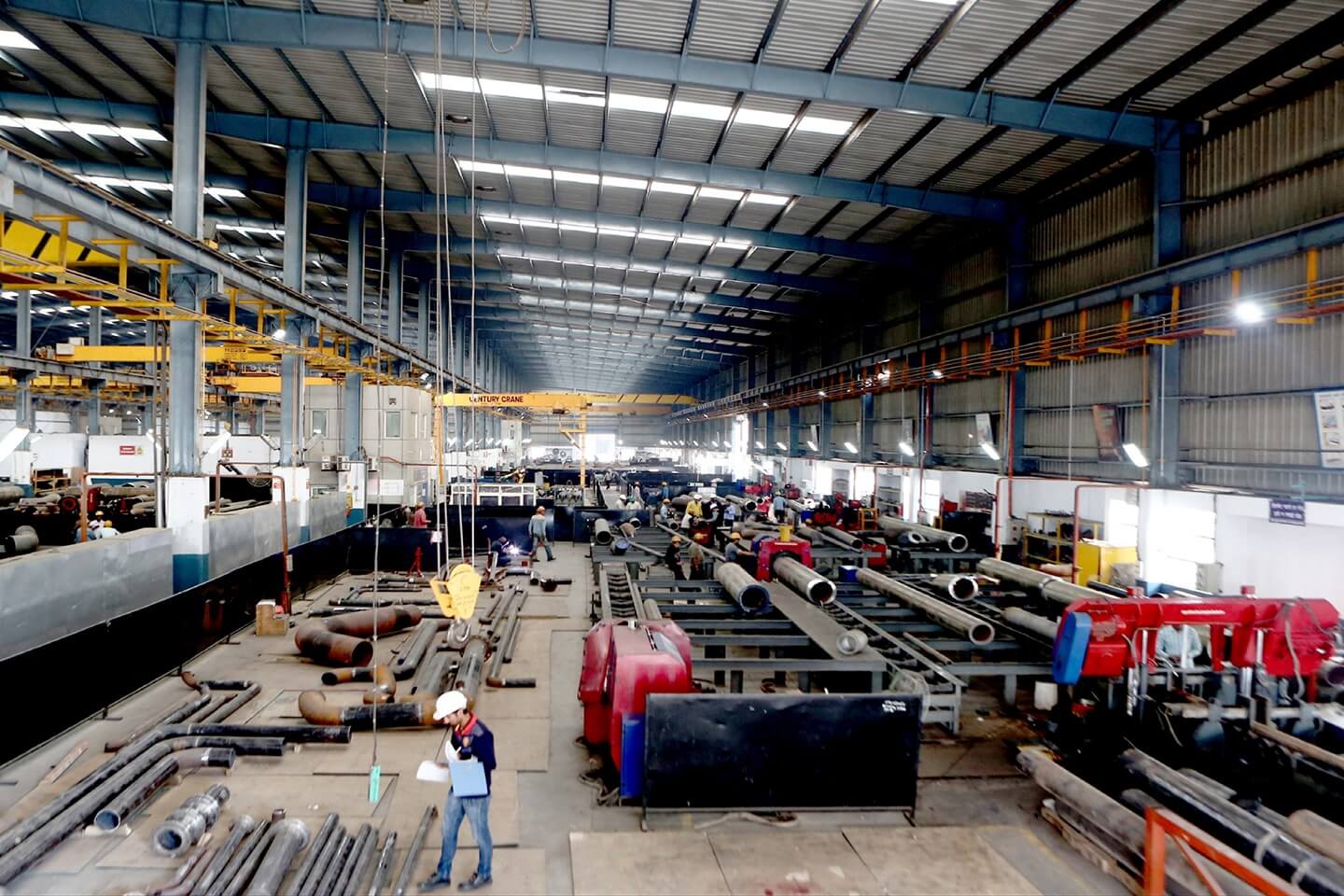
Fabrication Techniques / Processes
- Welding: Traditionally manual welding was the default welding process deployed. With the growth in scale of welding, manual welding became uneconomical (due to cost & time constraints) leading to the development of automatic welding technology. Today all large-scale fabricators use automatic welding, with varying levels of automation / technology sophistication.
We have been focussed on automating certain manufacturing processes and our Manufacturing Facilities are equipped with equipment such as fully automated robotic welding systems, semi-automatic shot blasting machines, automatic GMAW welding system and fully automatic high frequency induction bending machines having diameter of up to 48 inches.
We have introduced automation in our facilities for the manufacturing, design and fabrication of pipes. For instance, our Manufacturing Facilities are equipped with modern equipment and systems which includes fully automated robotic welding systems, in-house non-destructive facilities such as radiography test/ magnetic particle test, ultrasonic testing, liquid penetrant test, visual test, semi-automatic shot blasting machines and separate fabrication shops for stainless steel. However, in case there are any other new technological developments discovered that significantly decreases the cost of production, in order to compete effectively, we may be required to replace our existing machines with the new ones and thereby incur additional capital expenditure, which would have a material adverse effect on our financial condition and results of operations.
- Automatic Welding Process: Welding process using an automatic welding machine, primarily used for repeated welding in a factory assembly line. Depending upon the specific application and welding method, automatic welding can be segmented into automatic fusion welding, automatic pressure welding, and automatic brazing/ soldering.
- Robotic Welding: Robotic welding is the advanced form of automatic welding; wherein robotic technology is used to carry out the welding process. Typically, a robotic welding arm with multiple axes is used.